Die plates
Also known as : Die plates, Die face plate, Underwater pelletizer die plates, Extrusion die plate, Perforated granulation plates
Replacing a worn or damaged die face plate is a costly purchase. We offer quality equal to OEM parts at more competitive prices. Steel grade and hardness of the die plates are engineered for optimal cutting quality with the pelletizer knives. Our die plates can be fitted with:
- Coated surface
- Solid steel with nitrated cutting surface
- TC segments
Die plates are supplied including cone and cover plate. In case you do not have production drawings, our designers can help with production drawings based on your sample. Besides new die plates, we can also repair your die plate by replacing the TC segments.
Our die plates are engineered with precision and feature Tungsten Carbide inlays, ensuring exceptional performance and longevity.Die plates are supplied including cone and cover plate. In case you do not have production drawings, our designers can help with production drawings based on your sample. Besides new die plates, we can also repair your die plate by replacing the TC segments.
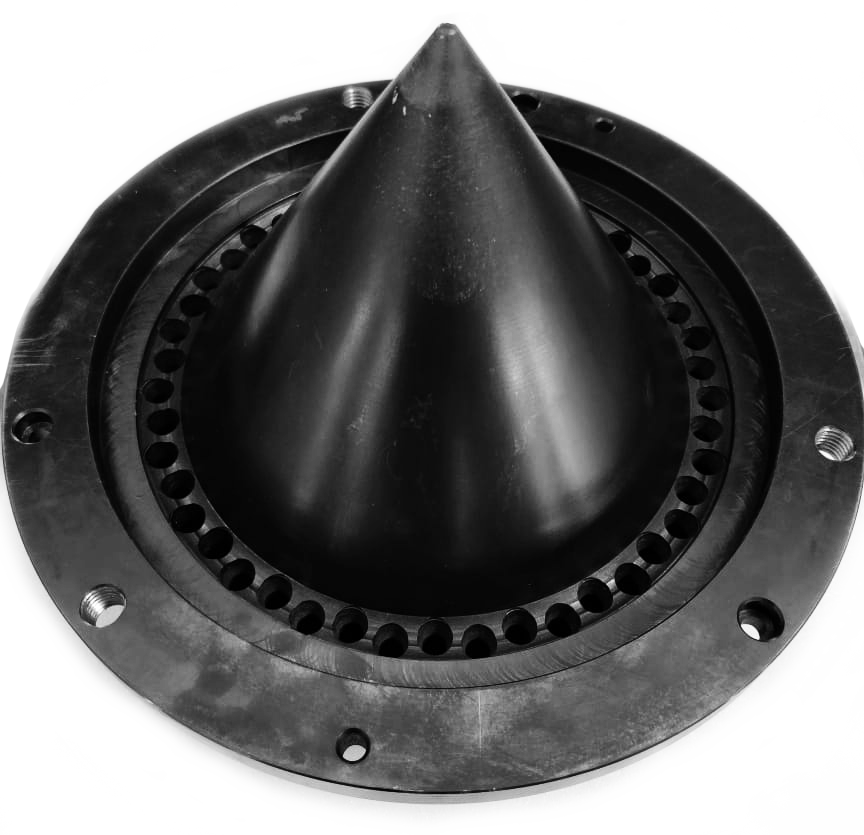
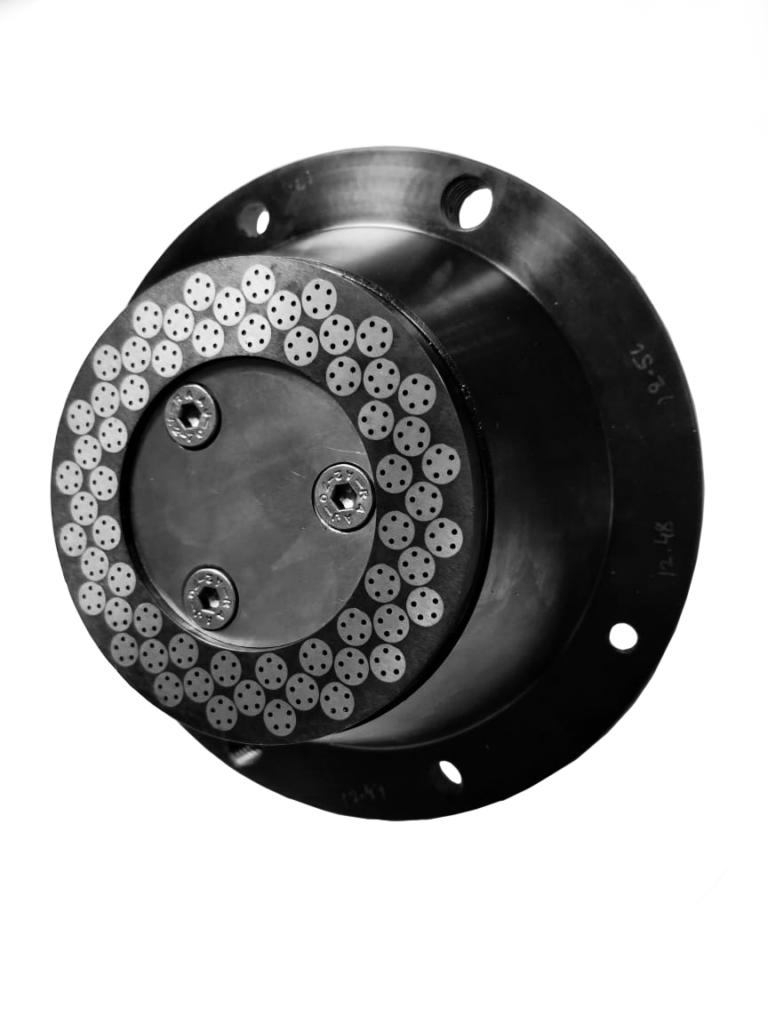
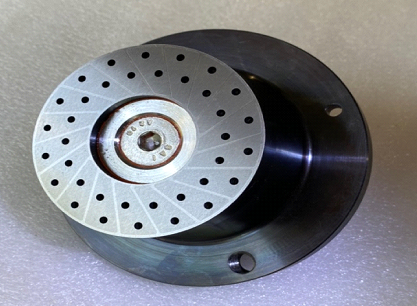
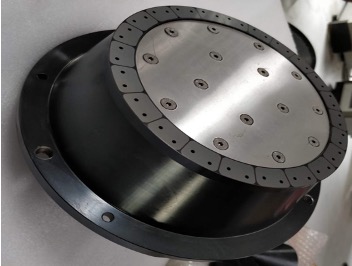
A water ring pelletizer die plate is a specialized component used in the plastic and polymer processing industry, particularly in pelletizing systems. These systems convert molten polymer into uniform granules (or pellets) for use in various applications.
Material and Durability:
- Made of materials such as tool steel or tungsten carbide inlays and TC coating for longevity.
- Withstands high temperatures and pressures during extrusion.
Advantages of Using a Water Ring Pelletizer Die Plate:
- Efficient Cooling: The water ring system ensures rapid cooling for smooth pellet production.
- Consistent Pellet Size: Precise die design contributes to uniform granule dimensions.
- Durability: High-quality materials like tungsten carbide inlays enhance wear resistance and extend service life.
This die plate plays a critical role in industries like plastic recycling, compound production, and polymer manufacturing, where pellet quality and consistency are essential.
Oil-heated die plates are specialized components in polymer extrusion and pelletizing systems designed to maintain consistent temperatures using a thermal oil circulation system. They are primarily used in processes where precise temperature control is critical to ensure the quality of the extruded polymer
Key Features of Oil-Heated Die Plates:
- Temperature Regulation:
- Heated by circulating thermal oil within channels or cavities inside the die plate.
- Provides uniform and consistent heating, preventing temperature fluctuations that could lead to uneven pellet formation or material degradation.
- Applications:
- Used in processes involving high-viscosity or temperature-sensitive polymers.
- Common in underwater pelletizers and other advanced pelletizing systems.
- Material and Construction:
- Made of durable materials like stainless steel or tool steel to withstand high operating pressures and temperatures.
- Often integrated with tungsten carbide inlays or wear-resistant coatings to enhance durability.
- Advantages Over Electrically Heated Die Plates:
- Uniform Heating: Oil provides even heat distribution, reducing the risk of hot spots or uneven material flow.
- Energy Efficiency: Oil heating systems can be more energy-efficient in specific industrial setups.
Reduced Thermal Stress: Offers gentle heating compared to electric methods, which helps prolong the die plate’s lifespan.
A strand die plate is a crucial component in polymer processing, particularly in strand pelletizing systems. This equipment is used to produce plastic pellets or granules by extruding molten polymer through the die plate in the form of continuous strands, which are then cooled and cut into uniform pellets.
Material Construction:
- Typically made from high-strength steels or equipped with tungsten carbide inlays to resist wear and high temperatures.
- Designed to withstand pressure and ensure consistent extrusion across multiple holes.
Hole Design:
- The size and number of holes are optimized for the type of polymer and desired pellet size.
- The uniformity of the holes ensures consistent strand dimensions for precise pellet cutting.